PROCESS OPTIMISATION AND INTEGRATION
In line with process digitalisation, Austria‘s leading manufacturer of varnishes, paints and wood preservatives ADLER has implemented digital data acquisition for raw materials in the pre-commissioning area. The employees in this section were equipped with mobile multifunctional sets from i.safe MOBILE (hand-held barcode scanner IS-TH1xx.1 and the intrinsically safe smartphone IS530.1) for the potentially explosive zone 1/21. The use of the Ex-protected high-performance scanner enables the automatic control of raw materials during the scanning process, reducing possible errors and faulty batches. The captured data is stored in a database, which ensures complete documentation and traceability of the production processes. The i.safe MOBILE partner ematric accompanied the project on the software side. The combination of comprehensive traceability of order status, monitoring of raw material processing and visual display of hazard warnings and work steps on the mobile device ensures that production at ADLER Lacke runs quickly and efficiently. The barcode scanner system thus makes a significant contribution to optimising processes, raising quality standards and ensuring the safety of employees.
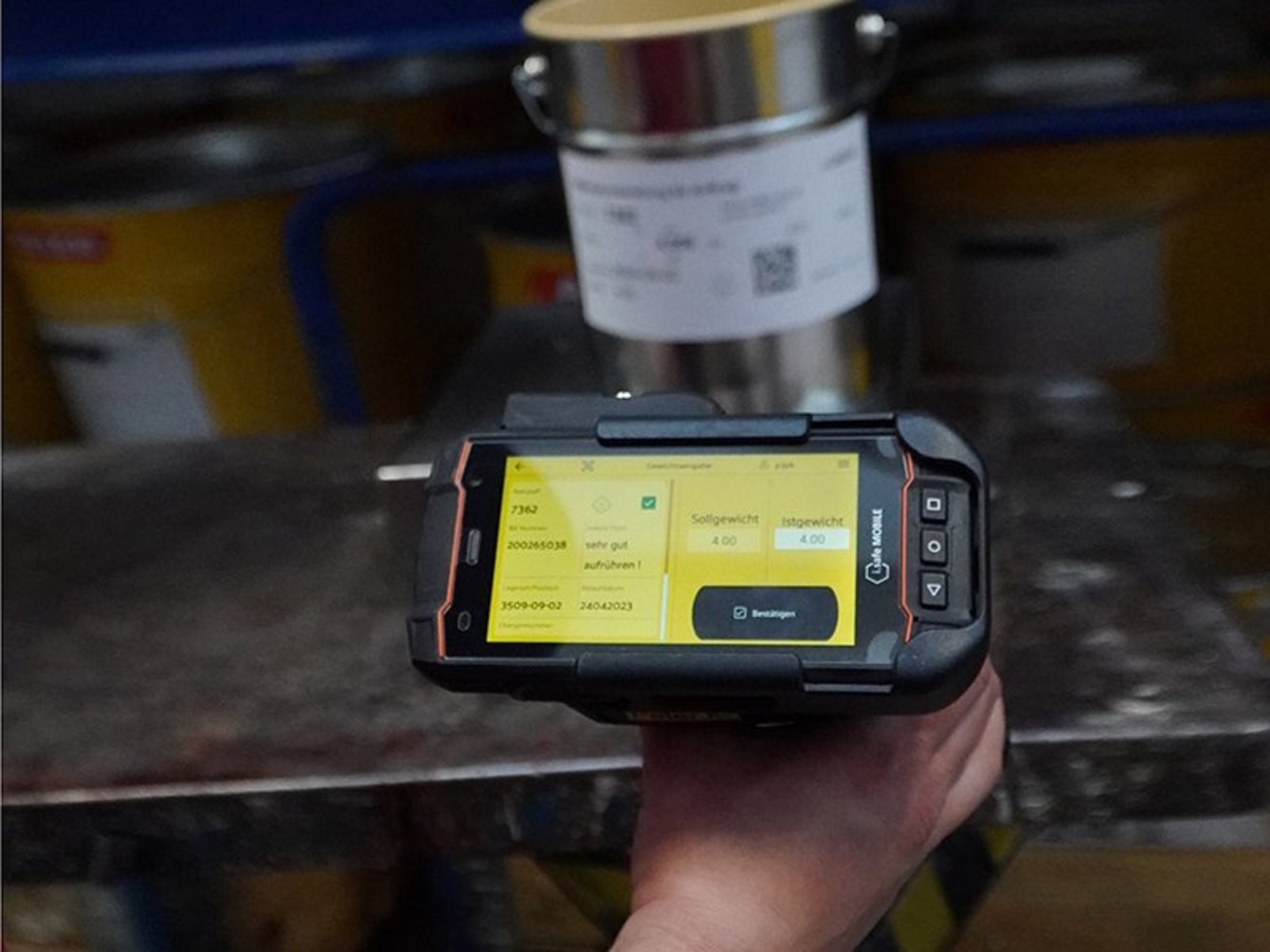
Implementation
The project was supported by i.safe MOBILE-partner ematric, who developed both, the software for the mobile handheld device as well as the integration software for this project. This made it possible to seamlessly integrate the barcode scanning system into ADLER Lacke‘s existing IT structure. The integration enabled smooth communication and cooperation between the IS-TH1xx.1 and other digital tools or machines in production. It is now possible to track the status of the order in real time. Each production step is precisely recorded, saved in the database and the employees always have full control over the order status. No production step can be forgotten or overlooked.
Fears of changes to the usual work processes in precommissioning were unfounded, as the very successful project for digitalising the data collection of raw materials in the family business, which has over 720 employees, has shown. The employees in pre-picking were digitally supported in their work and equipped with the mobile multifunctional sets consisting of a barcode hand scanner and industrial smartphone from i.safe MOBILE. The project was successfully implemented after only a short time: The number of incorrect batches decreased, efficiency increased.

Production at ADLER Lacke
Especially in production, the traceability of the processed raw materials plays a decisive role. With the help of the barcode scanner system, employees can quickly and precisely check which raw materials have already been processed and which still need to be used. In the precommissioning department at ADLER, the required raw materials or semi-finished products are compiled and weighed for each production order. Depending on the recipe, up to 20 different liquid or powder materials are contained here, with a total of 1,200 different stored raw materials and semi-finished products. Digitalisation improves the quality assurance of the manufactured products; possible mix-ups of the materials and the resulting costly incorrect batches are avoided.
The display of hazard warnings and work steps in visual form on the mobile multifunctional device is another valuable aspect of the barcode scanner system. During the production process, employees receive important information shown directly on their IS530.1 smartphone. This contributes significantly to occupational safety, as potential hazards and necessary work steps are visualised clearly and easily understandable. Employees are thus better informed and able to perform their tasks precisely, which increases overall efficiency and safety in the workplace.
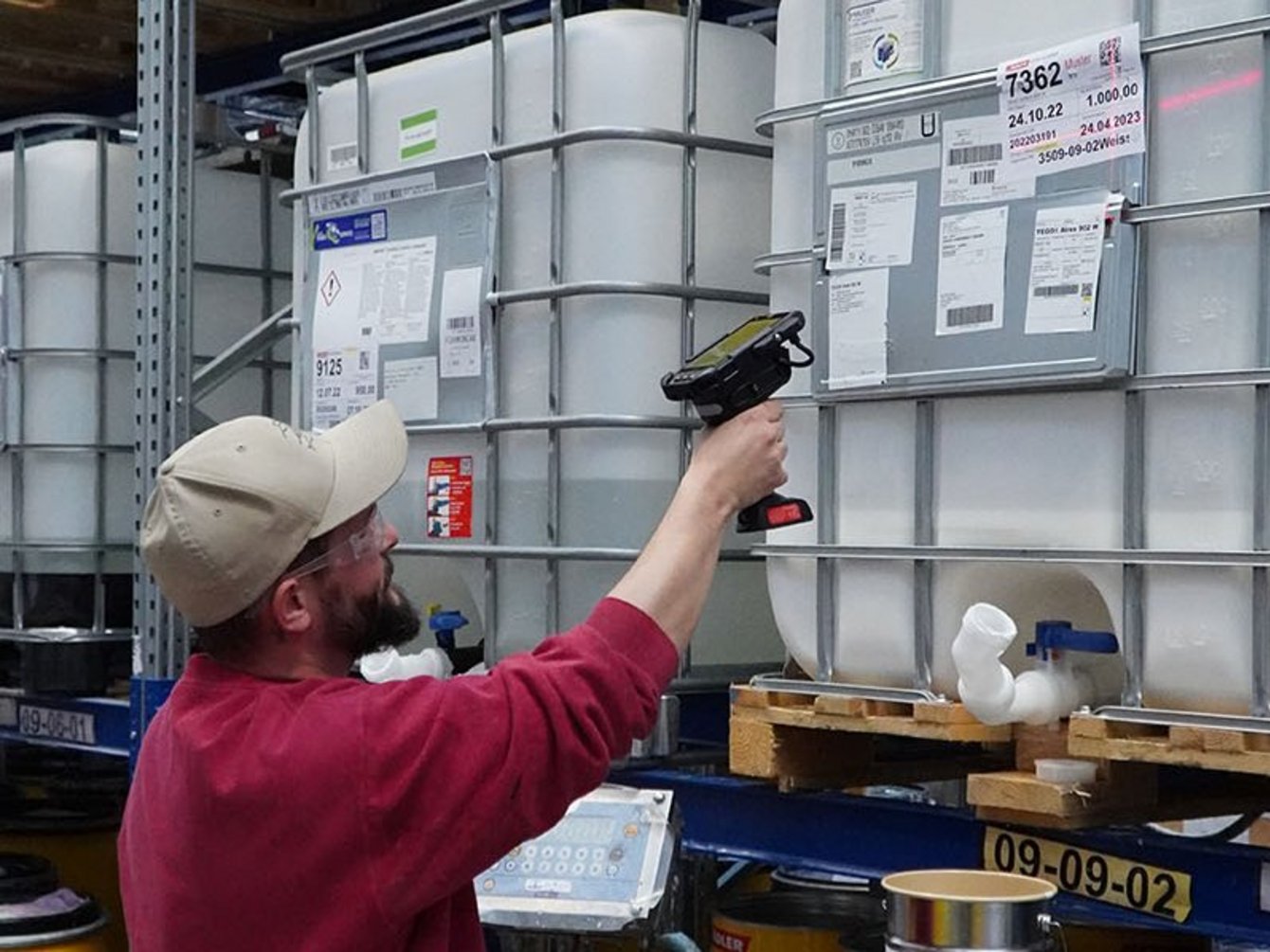
The multifunctional set in use
The employees have responded very positively to the new digitalisation project and job satisfaction has increased. After extensive training of the employees, each team member in pre-picking was equipped with a multifunctional device.
Each raw material is marked with a QR code on the production recipe; this is scanned and the employee is shown the exact storage location on the device display. In addition to saving an enormous amount of time, raw material mix-ups and the resulting incorrect batches are avoided. A QR code is also attached to the respective storage location of the raw material, which is scanned. In case of a „wrong scan“, a war ning is immediately displayed on the device. The mobile device also displays further information such as the expiry date of the raw material or special processing instructions.
From the product selection process for the trigger handle to the deployment of the devices, the implementation of the project took about six months.
„The scanners from i.safe MOBILE have changed our lives a bit. With the support of i.safe MOBILE, we were able to implement a project that speeds up and simplifies our work processes while reducing the error rate,“ explains foreman Christoph Wolf. „We have thus successfully taken another big step towards digitalisation.“
The project offers promising prospects for the future and is part of ADLER Lacke‘s comprehensive digitalisation strategy. The goal is to make the entire production process efficient and transparent. The tracking of raw materials and products is to be further improved, responsiveness to customer requirements increased and transparency for decision-making processes further expanded. In the next step, the digitalisation project is to be extended to the entire production: The main production steps up to filling will be digitally recorded, so that in future every employee will be able to view the production process in real time. The experience gained from the digitalisation project will also be incorporated into the detailed planning of the new raw materials logistics.
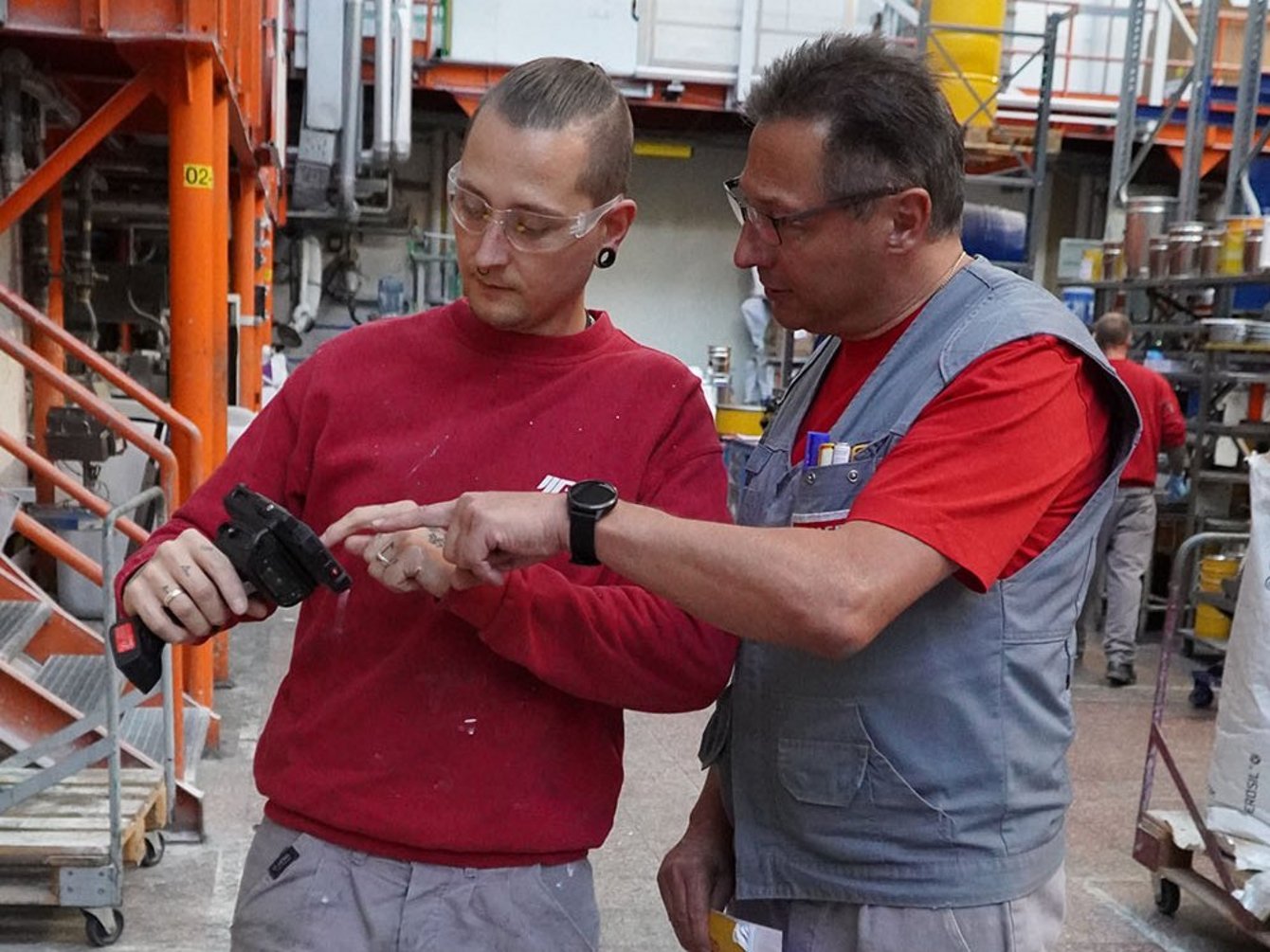
At ADLER, the protection and satisfaction of employees is a priority also with these measures. Digitisation is intended to sustainably increase productivity and strengthen ADLER Lacke‘s innovative power in the long term.
The barcode scanner project at ADLER shows how the use of modern technologies and a integrated digitalisation strategy can increase efficiency and productivity in a company. By using the Android™ Enterprise Recommended-certified IS530.1 device and combining it with an Android Enterprise-compatible MDM system, a high level of security and user experience is ensured.
Devices from Android Enterprise Silver Partner i.safe MOBILE stand for quality, robustness and security.
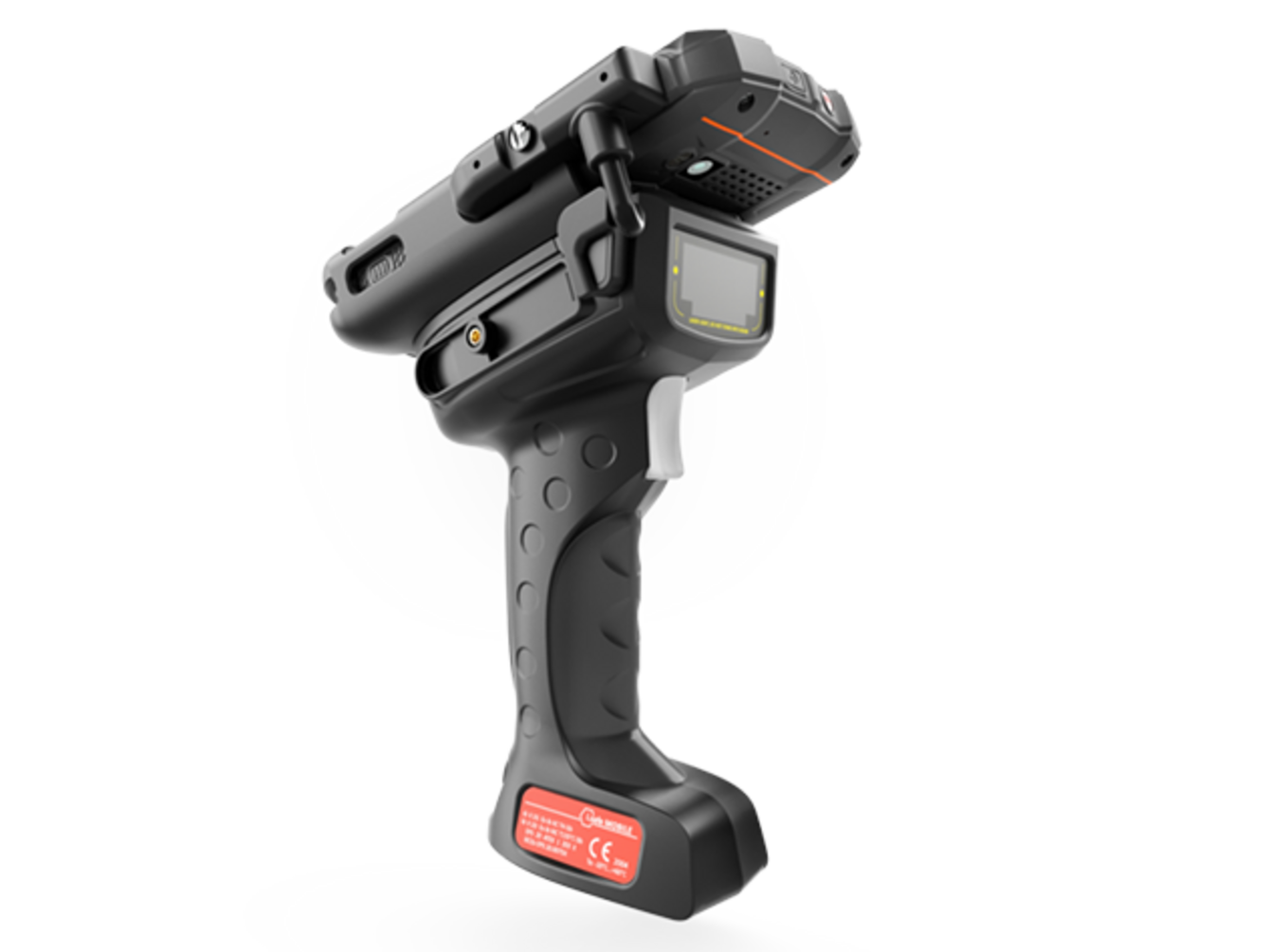
The mobile multifunction set
At ADLER, the mobile multifunction set consisting of the IS-TH1xx.1 hand-held barcode scanner and the IS530.1 industrial smartphone from i.safe MOBILE is in use and enables reliable data acquisition in hazardous areas for up to 18 m scanning distance.
Easy handling: The IS530.1 is plugged into the trigger handle, securely connected to the high-performance scanner via the 13-pin ISM interface and is ready for immediate use. The IS-TH1xx.1 does not require a separate battery or Bluetooth™ due to the direct interface connection with the smartphone. Using Zebra‘s reliable OEM imager scan engine, the scanner captures any 1D or 2D barcode – just by pressing the trigger. The available Mid Range variant is suitable for scans up to 6 metres, the Extended Range variant even for scans up to 18 metres. The barcode captured even under the most difficult conditions is immediately recognised as a keyboard input and further processed by the IS530.1.
The multifunction set is Android-based and, unlike alternative systems, guarantees secure, mobile data management.
ABOUT ADLER
With 720 employees, ADLER is Austria‘s leading manu-facturer of varnishes, paints and wood preservatives. Founded in 1934 by Johann Berghofer, this family business is now managed by a member of the third generation, Andrea Berghofer. Every year, 21,000 tonnes of paint leave the Schwaz plant and are delivered to customers in more than 30 countries worldwide. ADLER has sales subsidiaries in Germany, Italy, Poland, the Netherlands, Switzerland, the Czech Republic and Slovakia; their sole production site is the ADLER-Werk Lackfabrik in Schwaz, Tyrol (Austria). ADLER was one of the first companies in its sector to be 100% climate neutral (since 2018). The company has been able to reduce its carbon footprint to a minimum through a wide range of measures. ADLER offsets any unavoid-able residual emissions through the purchase of recognised climate protection certificates, thereby helping to finance new climate protection projects.
ABOUT ematric
Since 2007, ematric has been a pioneer in the fields of automation technology, mechatronics, robotics and IIoT. With a clear focus on the future, ematric is actively shaping the world of automation and digitalisation and realising innovative solutions for plants and work processes. ematric supports a wide range of customers worldwide – from large multinationals to small and medium-sized enterprises – in optimising production processes and increasing competitiveness.
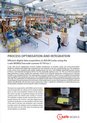